久しぶりに「ルアー作成方法」カテゴリの更新。
以前までの記事では、ルアーの作成方法を記載してました。
んで、当初の頃に比べて、若干作成方法にも手を加えているんです。
もちろん目的としては効率化であったり、強度UPであったり、仕上げの美しさであったり・・・。
さて久しぶりの、このカテゴリの更新ですが、お題は「強度UP」。
「強度」といっても、いろいろとありますが、今回はトップコーティングの強度UPについて書こうと思います。
私の作るルアーは基本的に以下の工程を得て作成します。
1:バルサ材の削りだし
2:成形
3:下地コーティング
4:塗装
5:トップコーティング
6:リップ、フック取り付け
って感じ。
で、下地コーティングで使用する材料は「セルロース」ですが
トップコーティングで使用する材料は「ウレタン」にしています。
ウレタンにしているのは、作成するルアーがクランクのため。
※ウレタンの特性として、セルロースと比べてコーティング塗膜が厚くなるっていうのと、弾力性があるっていうのがあります。
このため、クランクのように障害物にあたったりするようなルアーなんかはウレタンで作るのが適してます。
このウレタンのもうひとつの特性として、重ねてコーティング(ディッピングやドブ漬け)する場合、下のコーティング部分を溶かさず、そのまま上に乗っかる感じで、次の塗膜が形成されていきます。
ちなみにセルロースの場合は、下のコーティングを溶かしながら、上のコーティングを形成するので、完成後は1枚のコーティングになります。
なので、ウレタンでトップコーティングすると、最低でもドブ漬けを6~10回とかするので、ウレタンの層が6~10できるって感じ。
ここで何が問題かというと、単純にドブ漬けを繰り返していると、上にウレタンが乗っかるだけなので、衝撃によって剥がれる可能性があります。
本来ならばトップコーティングする場合は、はじめから最後まで、エアブラシで薄めたウレタンを吹き付けるってのが良いんです。
エアブラシで吹き付けることにより、塗膜の表面は微細な凹凸ができているので、重ねて吹き付けることによって
層と層がガッチリと組み合わさり、強度が増すんですな。
ただ、これだと20回くらい同じ作業を繰り返さないといけないので、あんまり効率的ではないんです。
んでは、どうするのか???
答えは簡単♪
塗膜に凹凸を作れば良いんです。
手順は簡単。
2~3回ディッピングしたルアー(もちろんちゃんと乾燥していること)の表面に、300番台以上の目の細かいヤスリや
耐水ペーパーで磨くんです。
ぱっと見ると、せっかくきれいにコーティング中のルアーが
傷だらけになっちゃうんですが・・・
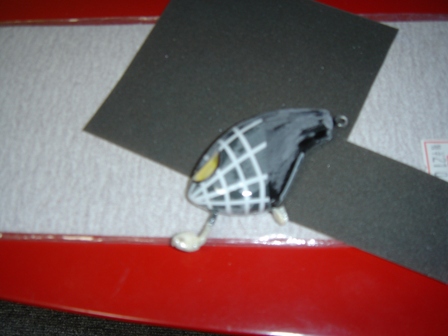
↑こんな感じ。
再度、ドブ漬けすると、あら不思議(笑)。
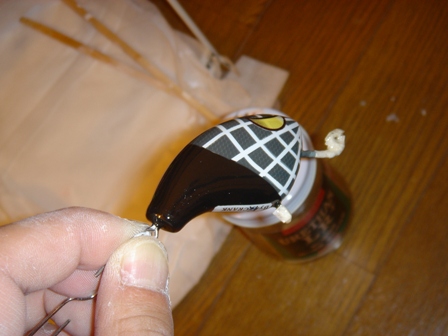
ちゃんと綺麗になります。
これより、塗膜に凹凸ができ、層と層がガッチリと組み合わさるので、強度がUPするというわけですな。
メリットとしては、強度UPのほかにも、微細な気泡だったりシワだったりをヤスリで削ることで
綺麗に目立たなくすることが可能です。
また、使い込むことで出来る「フックサークル(フックによるボディのキズ)」なんかも綺麗に直ります。
※フックサークルは使い込んでいる証拠!って感じで好きなんですが、あんまりひどくなると、ボディの木の部分にまでキズが入り、水が浸みてしまう可能性があるので、たまにやっています。
手間自体は若干増えるんですが、メリットが大きいので、最近作っているルアーには必ず、この工程を入れています。